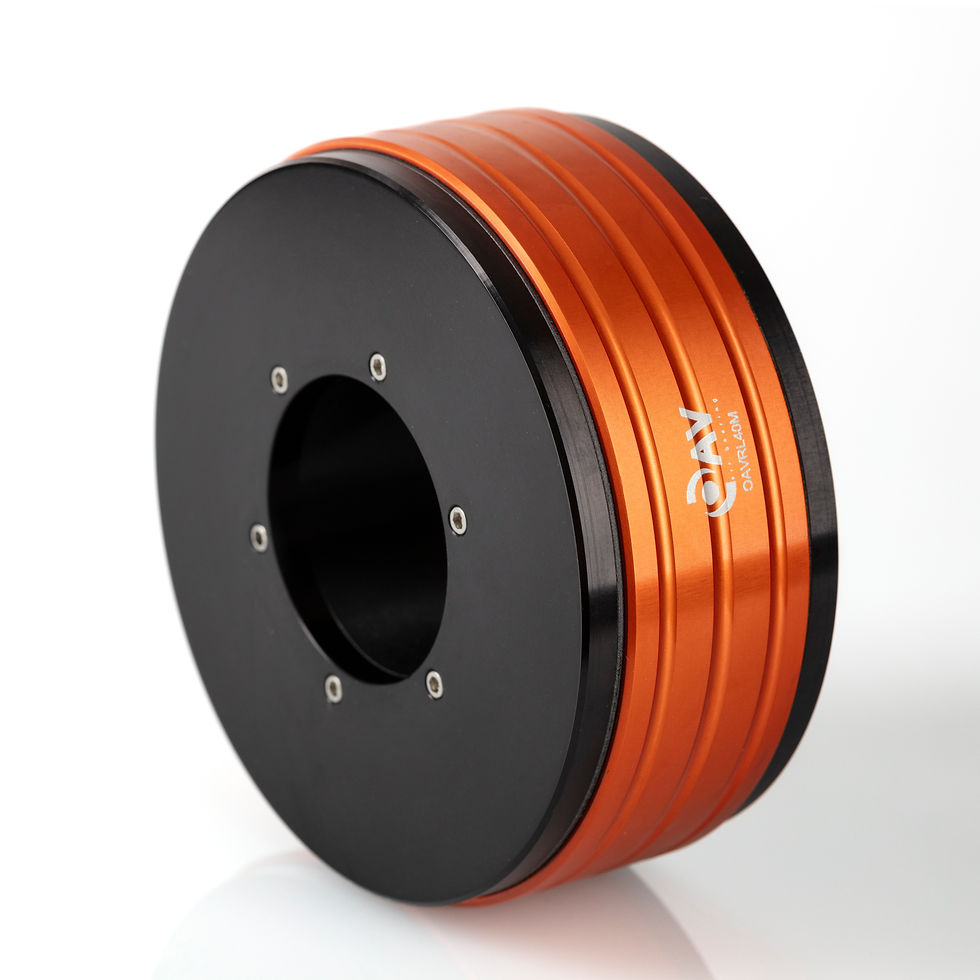
When calculating the critical speed of a shaft supported by air bearings, several key factors must be considered to ensure accuracy and reliability. Understanding these factors is crucial as they directly impact the performance and safety of the rotating machinery. Critical speed calculations help in predicting the point at which the shaft begins to resonate, leading to potential damage or failure.
In rotating systems, resonance occurs when the operating speed matches the natural frequency of the system, causing large amplitude vibrations. This can lead to excessive wear, noise, and even catastrophic failure. Therefore, accurately predicting the critical speed is essential to avoid these issues and ensure the longevity and reliability of the equipment.
Air bearings, with their high stiffness and minimal friction, provide significant advantages in high-speed applications. They reduce the wear and tear typically associated with traditional bearings and offer smoother and more stable operation. However, it is important to account for both the bearing properties and the shaft characteristics in the calculations.
This article outlines these considerations in detail and provides a step-by-step method for calculating the critical speed, including the effects of damping and friction. By following these guidelines, engineers can design systems that operate safely within the required parameters, avoiding resonance issues. Please contact OAV Engineers for any questions or concerns regarding these calculations.
Customer Considerations
1. Shaft Properties
- Material Properties: Young's modulus (E) and density of the shaft material.
- Geometry: Length (L), diameter, and the second moment of area (I) of the shaft's cross-section.
- Mass Distribution: Even or uneven mass distribution along the shaft.
2. Air Bearing Properties
- Stiffness: Air bearings often provide high stiffness, but this needs to be precisely known.
- Damping: Air bearings provide damping characteristics, which can affect vibration behavior.
3. Load Conditions
- Weight of the Shaft: The static deflection (δ) is influenced by the weight of the shaft.
- External Loads: Any additional loads applied to the shaft during operation.
4. Boundary Conditions
- Support Type: Whether the shaft is simply supported, cantilevered, or has other boundary conditions.
- Support Locations: The position of the air bearings along the shaft.
5. Operating Environment
- Temperature: Changes in temperature can affect material properties and air bearing performance.
- Pressure: The air pressure supplied to the bearings.
6. Dynamic Effects
- Rotational Speed: The speed at which the shaft is intended to operate.
- Resonance: Ensuring that operating speeds avoid critical speeds to prevent resonance.
7. Measurement and Validation
- Deflection Measurement: Accurately measuring the static deflection (δ) of the shaft.
- Experimental Validation: Testing the calculated critical speed with real-world measurements.
Calculation Steps
1. Measure or Calculate Static Deflection (δ)
Use the formula for deflection of a simply supported beam if applicable:
δ = (5WL³) / (384EI)
- W is the weight of the shaft (N).
- L is the length of the shaft (m).
- E is Young's modulus (Pa).
- I is the second moment of area (m⁴).
2. Calculate Effective Stiffness (K_eff)
Determine the stiffness of the shaft (K_shaft) and the air bearing (K_bearing).
Use the formula to calculate the effective stiffness: K_eff = 1 / (1/K_shaft + 1/K_bearing)
3. Calculate Static Deflection (δ)
Use the effective stiffness (K_eff) to find the static deflection of the shaft: δ = W / K_eff
4. Calculate Critical Speed
Use the deflection (δ) in the critical speed formula:
Critical Speed (in RPM) = (1 / 2π) √(g / δ) 60
g is the acceleration due to gravity (9.81 m/s²) and
δ is the static deflection (m).
Damping and Friction Considerations
Air bearings introduce minimal friction, but any residual friction can introduce damping into the system. Damping reduces the amplitude of vibrations at and near the critical speed, making the system more stable.
5. Calculate Damping Ratio (ζ)
Estimate or measure the damping coefficient (C).
Calculate the mass (m) of the shaft.
Use the effective stiffness (K_eff) to find the damping ratio: ζ = C / (2√(mK_eff))
6. Calculate Damped Natural Frequency (ω_d)
Use the formula for the damped natural frequency: ω_d = ω_n √(1 - ζ²)Where ω_n is the undamped natural frequency (critical speed).
7. Convert to RPM
Convert the damped natural frequency to RPM:
Damped Critical Speed (in RPM) = ω_d / 2π × 60
Example Calculation
Assuming you have the following data:- Weight of the shaft (W): 100 N- Length of the shaft (L): 1 m- Young's modulus (E): 210 GPa (for steel)- Second moment of area (I): 5 × 10⁻⁶ m⁴- Stiffness of the shaft (K_shaft): 2 × 10⁶ N/m- Stiffness of the air bearing (K_bearing): 1 × 10⁶ N/m- Damping coefficient (C): 100 Ns/m- Mass of the shaft (m): 10 kg
Calculate Static Deflection (δ)
1. Calculate Effective Stiffness (K_eff): K_eff = 1 / (1/2 × 10⁶ + 1/1 × 10⁶) ≈ 0.67 × 10⁶ N/m
2. Calculate Static Deflection (δ): δ = 100 / 0.67 × 10⁶ ≈ 1.49 × 10⁻⁴ m
Calculate Critical Speed
Critical Speed = (1 / 2π) √(9.81 / 1.49 × 10⁻⁴) × 60 ≈ 1281 RPM
Calculate Damping Ratio (ζ)
Damping Ratio (ζ): ζ = 100 / (2√(10 × 0.67 × 10⁶)) ≈ 0.0193
Calculate Damped Natural Frequency (ω_d)
Undamped Natural Frequency (ω_n): ω_n = √(0.67 × 10⁶ / 10) ≈ 259.16 rad/sDamped Natural Frequency (ω_d): ω_d = 259.16 √(1 - (0.0193)²) ≈ 259.10 rad/s
Convert to RPM
Damped Critical Speed (in RPM): ω_d / 2π × 60 ≈ 2474 RPM
By understanding and accurately calculating the critical speed of shafts supported by air bearings, engineers can prevent resonance-related issues, ensuring the system operates smoothly and reliably. This critical calculation not only enhances the performance and longevity of rotating systems but also minimizes maintenance costs and prevents unexpected downtimes. For further assistance or inquiries, please reach out to OAV Engineers. We are committed to providing the expertise and support necessary for your engineering success.